Significance of labeling in the supply chain
We discuss how implementing standards like GS1, using machine-readable labels, and EDI can optimize the supply chain.
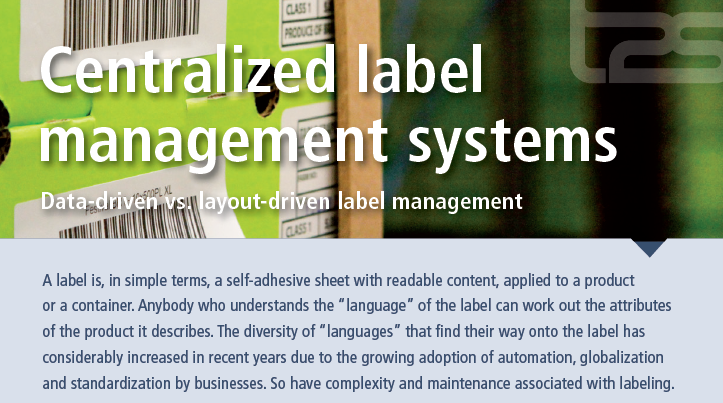
Centralized label management systems
Data-driven vs. lay-out driven label management
The supply chain can be optimized by implementing standards, using machine-readable labels, and making use of EDI. The label is the carrier of the identification within the supply chain, and therefore a crucial link in the chain.
The complexity of the labeling process depends on legal provisions, customer requirements and factors internal to the organization. With an increasing number of products, facilities, and customers comes an increasing need of flexibility and manageability of the labeling process.
A label is, in simple terms, a self-adhesive sheet with readable content, applied to a productor a container. Anybody who understands the “language” of the label can work out the attributes of the product it describes.
The diversity of “languages” that find their way onto the label has considerably increased in recent years due to the growing adoption of automation, globalization and standardization by businesses. So have complexity and maintenance associated with labeling.
This paper first portrays the impact of that increase in complexity on labeling, and thus on the software solutions that produce the labels. Next, it outlines the different types of centralized labelmanagement solutions that can be linked to an ERP system and examines the reasons why this kind of functionality is rarely integrated into the ERP system itself. In conclusion, the different types of solutions are weighed up against each other.
Significance of labeling in the supply chain
A typical organization stores basic data about a shipping unit, such as productname, batch number, recipient name or address, in an ERP system. Once this unit begins its journey through the supply chain, information is added to that data bit-by-bit in order to properly identify and track it throughout its journey.A selection of these information bits is expressed on a label, which is applied to the product or its packaging. By encoding the identifying values for the unitin a bar-code, the label can be scanned, and is therefore machine-readable.
One of the common standards that have been developed to that effect is the GS1 standard (formerly knownas EAN-International). The organization behind that standard counts more than a million member businesses in over 30 industries and 104 countries.
What such standards do is – simply put – bring the processes of suppliers and recipients closer together. The exact information that has to be added and maintained to comply with the GS1 standard can be found in the specification documents on the GS1 web site.
However, one element of the communication protocol embedded in GS1 worth mentioning is the Serial Shipping Container Code, commonly referred to as the SSCC. This 18-digit code can be expressed on a label as a bar-code, and is used to identify a pallet or a container. In addition to the labeling effort, the supplier can send a matching despatch message to the recipient via Electronic Data Interchange (EDI).
The despatch advice message contains information that conforms to the standard and the possible agreements between supplier and recipient. The SSCC bar-code makes it possible to track the shipment throughout the supply chain. When the recipient scans this bar-code at the time the goods are received, the embedded code is matched to the despatch advice message that has been received previously, providing the recipient with a detailed overview of the contents of the pallet or container.
While it is possible to use the SSCC without the associated despatch message, doing so increases the risk of errors and decreases the efficiency of the process.Most ERP systems support the use of SSCCs for both suppliers and recipients, and expose interfaces allowing to receive and store despatch messages, and to link them to an SSCC. When a pallet or a container is delivered, warehouse staff can scan the bar-code printed on the label, and are then presented with all characteristics of the container or pallet in question.
Most ERP systems support the use of SSCCs for both suppliers and recipients, and expose interfaces allowing to receive and store despatch messages, and to link them to an SSCC. When a pallet or a container is delivered,warehouse staff can scan the bar-code printed on the label, and are then presented with all characteristics of the container or pallet in question.
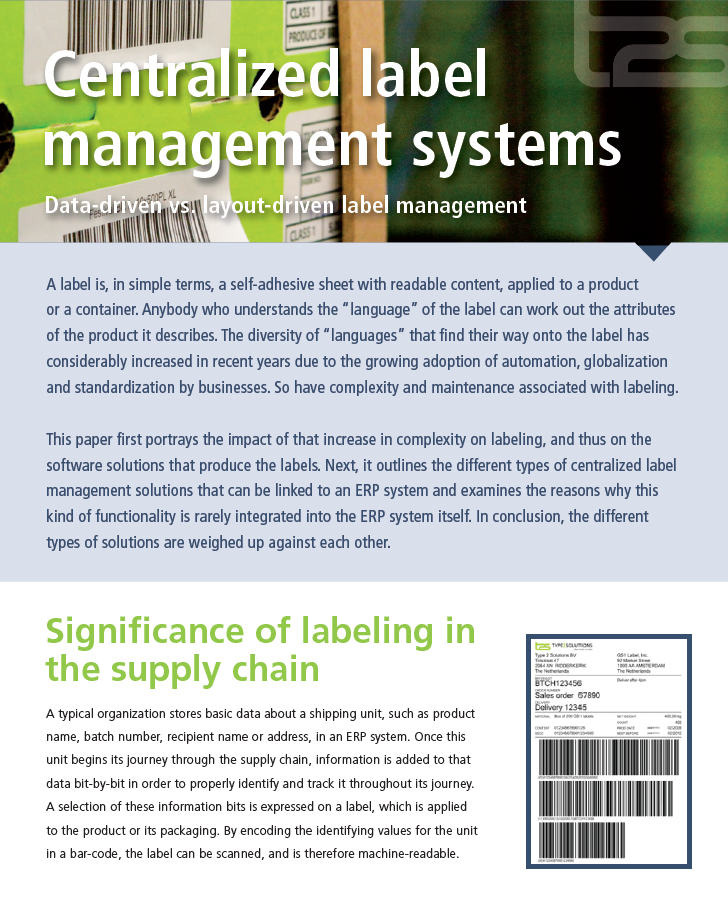